Now more than ever, manufacturers are looking to lower production costs without sacrificing quality. One way to achieve this is by implementing production process optimization systems. Today, we’ll take a look at how these tools help companies achieve their increasingly demanding production efficiency and profitability goals.
Before we dive into the technology, let’s take a quick peak into the past. The concept of quality control stretches back around 100 years, when statistics were first applied to controlling production processes. Keep in mind, this was half a century before computers become widely available and affordable. Imagine that! A time when manufacturers implemented quality programs without the help of spreadsheets or commercially available optimization platforms. There was no alternative: production data was collected and crunched manually.
While technology has come a very long way since then, some remnants of the “old ways” still linger. Companies will still perform aspects of their reliability and quality control programs manually. While the machines now generate data, for many, the optimization process still relies on people to collect it. Technicians walk the production floor on scheduled routes, from machine to machine, collecting data. Then they take it back to their desks to share or analyze it themselves. This is inefficient, and doesn’t have to be the case, thanks to production process optimization solutions that are readily available today.
How Do They Work?
Simply put, these platforms primarily monitor, and in some cases, control manufacturing processes. They relay actionable data in real time, thus increasing efficiency, reducing waste, and solving other issues. Whether it’s an enterprise level solution or something more budget-friendly, they generally work the same way. The process starts when these systems automatically collect data from any machinery that generates it. This data is then processed, and reported, and can also trigger alerts. These alerts can be extremely valuable, as they can help operators manage a problem quickly - before it grows into a much bigger, costlier one.
Enterprise level solutions can be very powerful, but tend to come with a larger price tags and learning curves. As such, they are generally more suitable for large national and global manufacturers. For smaller and medium sized operations, or perhaps larger ones looking to solve a more specific challenge, solutions such as B&D’s OptiPro are available.
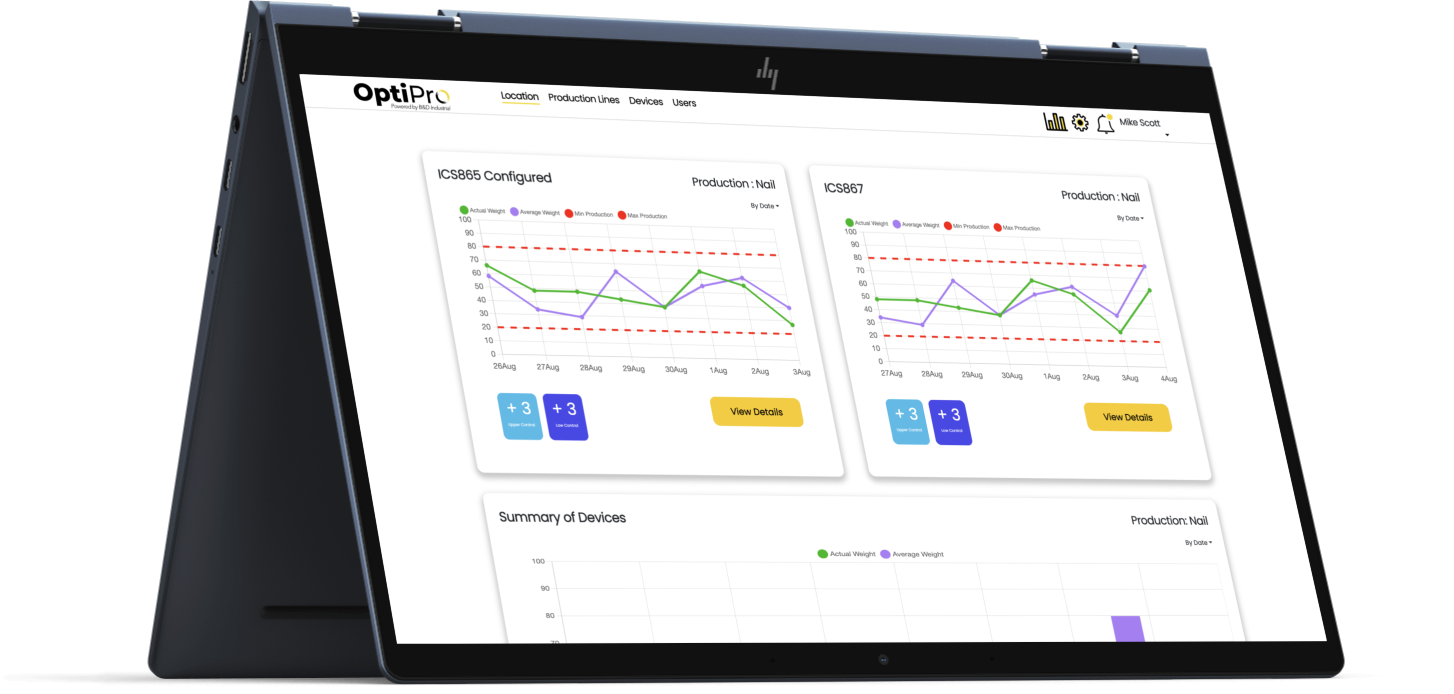
Benefits
There are many advantages to implementing a production management system besides increased efficiency. The list grows longer when considering an automated platform as a replacement for a manual process. Companies can:
- Monitor production in real time
- Quickly determine time and cause of metric deviation to mitigate losses, with the delays associated with manual processes
- Produce more consistent, higher quality product
- Improve production efficiency with the same or reduced head count
- Closely monitor ingredient/environment settings
- Eliminate waste of raw materials and end-product
- Reduce likelihood of errors due to manual data collection
- See what’s happening, without standing in front of the machinery
- Allows for central monitoring of processes across one or many locations
Features
OptiPro makes it easier to track, monitor and analyze production data. It has many other attractive features, including:
- Lower cost than enterprise systems
- Easy to implement
- Visual browser-based dashboard that allows you to record, log and display data where you have an Internet connection
- It’s brand-agnostic - the equipment being monitored can be from different manufacturers
- Anomaly / metric deviation alert/notification from pre-determined metric (e.g. weight, size)
- Allows users to set custom date range of data log to see production trend data
- Exports data in .cvs file for analysis to business intelligence platform at custom defined intervals
Flexibility is at The Core
One of the best aspects of production optimization systems is flexibility - they can be used to monitor an extensive range of machinery and processes. For instance, OptiPro is used to collect and analyze production scale data for food and beverage manufacturers. By doing so, operators can be certain that ingredient levels are accurate and within acceptable ranges. This helps prevent waste and ensure that the product is consistent. We all know that often, too much or too little of any ingredient can impact the flavor of something we are drinking or eating.
This is certainly the case for another customer who produces single-serve instant coffee. For this use, OptiPro monitors the oxygen content in the packets, in addition to overall weight. If the oxygen level is out of range, the flavor profile of the product can be significantly altered. OptiPro helps make sure that consumers are satisfied and not surprised, and can enjoy a consistently flavorful cup of coffee.
So, What Are You Waiting For?
These are just a few of the many examples of how production process optimization platforms can be applied to help manufacturers achieve their efficiency and profitability goals. If you haven’t implemented one yet – now is the time. By doing so, you can quickly reduce waste, improve overall productivity, and remain competitive in challenging times.